Ball Balancing Table
Balancing a ball on a table in a desired position is one of the most important and classical problems of control theory. Altair, partnering with ACROME, promotes the unique experience of a digital twin mechatronics simulation and hands-on experiment platform to teach and learn model-based controller design concepts with a 3D+lD system co-simulation engine.
The Ball Balancing Table (BBT) is a well-known kit for all mechatronics enthusiasts. Even if it might appear quite simple, it allows to investigate many aspects of control, for example anti-windup scheme for PID control.
The Ball Balancing Table (BBT) is a well-known kit for all mechatronics enthusiasts. Even if it might appear quite simple, it allows to investigate many aspects of control, for example anti-windup scheme for PID control.
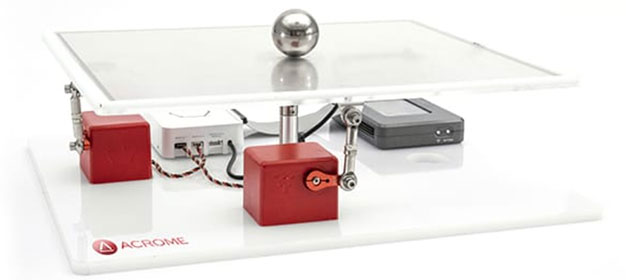
Explore MoreSales Enquiry
The main parts of the BBT kit are:
The main parts of the BBT kit are:
- Power Supply
- Controller (Arduino)
- RC Servos
- 2D resistive touch screen
- Steel Ball
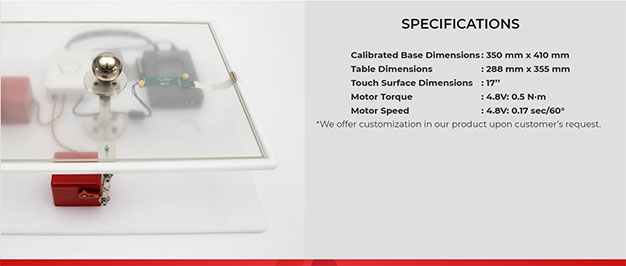
Features | |
---|---|
Assembled and ready to control plant with the integrated power unit. | Getting Started Program with rich Graphical User Interface for out-of-the-box user experience |
Implementation of advanced digital control techniques | Fully compatible with Altair Activate |
Fully documented system models and parameters provided for Altair Activate. | Ball position feedback using a high precision touch surface (camera based feedback optional) Actuating the table by RC servo motors, which are familiar to students. |
Rectangular and circular path options are integrated in the software. | Enables students to create their own real-time algorithms. Open architecture with extensive courseware, suitable for undergraduate courses for engineering disciplines related to control systems. |
Altair Activate
Altair Activate® software is an open & flexible tool for rapidly modeling and simulating products as multi-disciplinary systems in the form of 1D models (expressed as signal-based or physical block diagrams), optionally coupled to 3D models. Recently, it can also run hardware in the loop simulations, making it a perfect platform to develop mechatronic systems, such as:
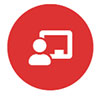
Teachers
Prepare your students to hit-the-ground-running in their work as mechatronics engineers!
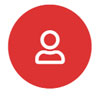
Students
Get the premier mechatronics jobs! As an explorer, empower yourself with the next generation engineering tools to innovate better and faster.
STARTER KIT | EXPANSION KIT |
---|---|
Hardware+ Courseware | Hardware+ Courseware |
Teaching License of Software | |
Initial Setup Help and Training (via web) |
- Only l Starter Kit is needed. If you already have the Altair software, you need only purchase Expansion Kits.
- Software License includes: Altair Compose®, Altair Activate®, Altair MotionSolve™ & MotionView™.
- All software apps can be installed and run on student computers and/or on school computers.
Features | |||
---|---|---|---|
Components of Ball Balancing Table | Fundamentals of PWM |
System Modelling |
Feedback in Control Systems |
RC Servo Motors | PWM Signaling Theory | Lagrangian Method | Reading Ball Position from Touch Sensor |
Touch Sensor | Generating PWM Signals Driving RC Servos with PWM Signals | Newton’s Law of Motion | Derivative Filtering |
Controller | Modeling of Actuator | ||
Acrome Power Distribution BoxMechanics of the System | Obtaining Transfer Function | ||
Performance Measure |
Control System Design |
Control System Verification | |
Time Domain Characteristics | Design of Linear Controllers | Frequency response analysis | |
Steady State Response and Steady State Error | PID controller and Fuzzy Logic Controller | Experimental Bode Diagram | |
Comparing the Simulation and Real System Responses for Different Controllers | Cut-Off Frequency Determination |
The following is the typical workflow for a typical BBT experiment
The closed loop system can be easily modeled in Altair Activate through this block diagram:
The last step is to test and validate the controller with the real BBT kit. This means that we are performing a hardware in the loop simulation.
As you can see the digital twin and the real BBT kit behave almost the same:
Detailed Proposals
We at ESS have meticulously compiled an out-of-the box – Robotics Test Rig with necessary Model Based design glue logic. Click below to download the Detailed proposal, Lab Manual, Lab Courseware, List of Experiments.
We can arrange a short live online demo of HIL simulation control of robotics kit at your convenience.
We can arrange a short live online demo of HIL simulation control of robotics kit at your convenience.